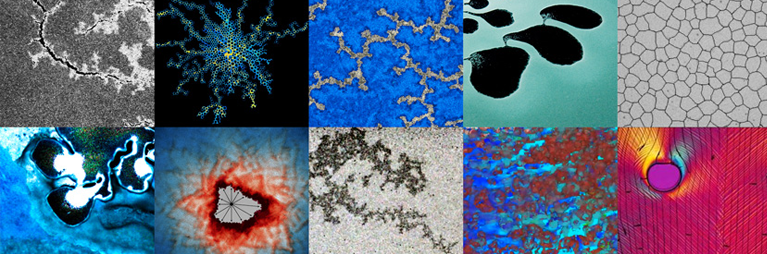
Engineering Systems
Focus of our research
Led by Prof Manus Henry, our group combines analytical, experimental and numerical methods to develop innovative models and solutions for a variety of environmental and industrial challenges, where fluid mechanics is key.
The Group has extensive experience in a variety of applications. These include geophysical fluid dynamics, porous media, industrial flow measurement, reservoir modelling and metering for Carbon Capture and Storage, and the risks from space travel to planetary protection.
Our work ranges from microfluidics, filters, microfabrication and biological flows (nanometres to centimetres) to water and energy resources and geo-hazards (metres to kilometres), to outer space (kilometers to astronomic units (AU) and beyond…)
Contact
To find out more about our research, please contact Professor Manus Henry.