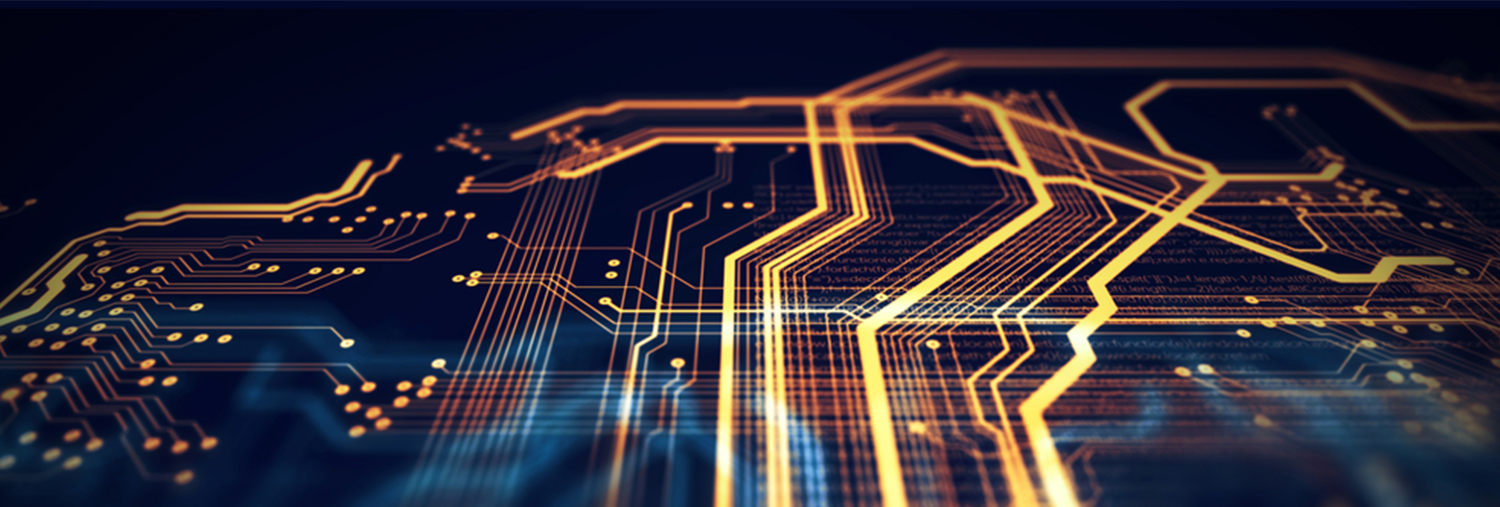
Stevenage Circuits
Company/Client
Stevenage Circuits Ltd (SCL)
Product/Service or Team utilised
KTP
The Challenge
The client’s challenge was to address commercial and technological challenges faced by the UK, EU and global PCB industry.
With technology advancing, in particular the component packaging device technology, the need for miniaturisation in the field of high density interconnect (HDI) PCBs has been increasing. As the increase in packaging densities continues, the device footprints will eventually reduce to a point where the PCB fabrication technology used by SCL (prior to the KTP) will no longer be capable of meeting requirements.
A KTP with Coventry University was seen by SCL as an ideal mechanism to develop new PCB manufacturing processes with smaller component sizes.
The Solution
Anjali Krishnanunni was recruited by Coventry University to spearhead a 2-year KTP project for SCL. Through the KTP, SCL were also able to access the research expertise of Dr Andrew Cobley and Narinder Bains, based within the Functional Materials Research Group at the University.
The aim of the project was to improve manufacturing capability to meet the future requirements of the electronics industry, particularly for high reliability military-aerospace grade HDI (high-density-interconnect) PCBs.
This has resulted in:
- Alternative manufacturing processes have been developed.
- SCL have been successful in deploying the new technology enhancements into programmes outside of the KTP, generating sales for the company.
- The dissemination of the technologies within SCL have provided its workforce with additional skills. This improvement has enabled SCL to undertake difficult work whilst maintaining high yields, representing an overall costing saving to the company.
- As the knowledge gained from the KTP has been embedded into the company, SCL are now able to seek out opportunities for the potential inclusion of their new manufacturing processes, widening their scope within the high value end of the marketplace.
- The KTP has changed the way SCL addresses and introduces new processes, and how they measure, compile and document the results.
- SCL now have new found confidence to review other potential research opportunities.
- Since the initiation of the KTP, SCL have held discussions with organisations regarding devices for the Medical, Defence and Agrochemical sectors, all of whom have expressed an interest in PCB structures with ultra-fine feature sizes, high density interconnect and extremely low surface topography – precisely the attributes addressed by the KTP.
The Associate presented her work at the Institute of Circuit Technology Annual Symposium and the EIPC Conference.
The KTP between SCL and CU has been very rewarding due to the good collaboration between the partners and the associate. Leading edge science in Printed Circuit Board manufacturing could not have been undertaken otherwise without the KTP project. The project was commercially driven from the onset and has maintained this throughout the project duration. This commercial drive has maintained the commitment of the industrial partner in very difficult trading conditions who are now benefiting from real commercial interests and orders resulting from the outcomes of the project.
Narinder Bains, Academic Supervisor