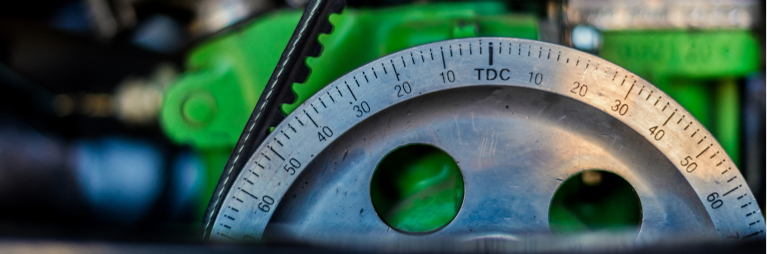
Remanufacturing Pathways (REMANPATH)
Creating learning materials to help SMEs develop remanufacturing competencies and business models.
Funder
EIT Raw Materials
PI and Project Team members
Sally Dibb, CBiS (Principal Investigator)
Sinead Ouillon, CTPSR (Co-Investigator)
Dr Helen Roby , CBiS (Co-Investigator)
Project Lead
Teknologian Tutkimuskeskus VTT (Technical Research Centre of Finland Ltd. VTT)
Project Overview
Professor Sally Dibb, Dr Helen Roby and Sinead Ouillon, between 2018 and 2020, worked with European partners to develop learning materials to support Small and Medium Size Enterprises (SME) in developing remanufacturing competencies and business models. The project was funded by the European fund, EIT Raw Materials KIC and led by the research institute, VTT in Finland in partnership with TU Delft in the Netherlands; Grenoble INP and Université Grenoble Alpes in France; Wuppertal Institut in Germany; and Oakdene Hollins, who run the European Remanufacturing Network in the UK
RemanPath built on the results of a previous Horizon 2020 research project, the European Remanufacturing Network. The aim of RemanPath was to create learning materials to support SMEs to develop competencies in remanufacturing. The learning materials were designed and tested through a series of workshops run by the partner organisations. These workshops also involved case study presentations, with businesses already engaged in remanufacturing telling their story of remanufacturing and the pitfalls and successes they had encountered. Qualitative and exploratory research was undertaken as part of the project to understand the triggers and barriers to remanufacturing, identify possible approaches to encourage more businesses to become remanufacturers and the channels for delivery of these approaches.
The CBiS research team ran two workshops in the UK to test out different formats of engaging businesses in remanufacturing and the learning materials. The first was a half-day workshop that took place at the Coventry based RDM Automotive, a manufacturer of autonomous pods, attracting SMEs, predominately from the automotive sector. The workshop included case studies from MCT Reman Ltd, an automotive remanufacturer and PSS, a steering and hydraulics remanufacturer. The second workshop at Silverstone Racetrack tested a different format, where the principles of remanufacturing were introduced to a wider audience as part of a daylong event that explored the transition to electric vehicles. The CBiS team have also been responsible for developing the ‘Go-to-Market’ strategy and marketing materials for the project to help with its long-term sustainability. The marketing materials include a short explainer video, newsletters reporting the work of the team and a brochure that includes an explanation of what remanufacturing is, the benefits of remanufacturing and some short case studies of remanufacturing in practice. These materials along with the learning materials were officially launched at the CBiS run launch event. The event showcased the key findings from the project, remanufacturing case studies from Brother UK and Microcab and the research of the Centre for Low Carbon Propulsion Systems (C-ALPS).
Key Findings
- Running workshops for SMEs concentrating solely on remanufacturing was a ‘hard sell’, partly because many did not understand the relevance of remanufacturing to them.
- Running workshops as part of larger events focusing on broader sustainability-related topics, was more successful in gaining interest and reaching a larger audience beyond manufacturers.
- Those beyond manufacturing, including organisations that support SMEs in developing business models, for example the Chamber of Commerce, showed interest in the potential of remanufacturing to support sustainability and business growth.
- Including real-life case studies in the workshops created enthusiasm for remanufacturing as the passion of the presenters became infectious.
Remanufacturing has clear benefits for business, society and the environment. However, only two percent of products in Europe are currently remanufactured. Despite this statistic, there is growing awareness of circular economy and shared ownership models, such as car pooling and product-as-a service, for example leased shared washing machines. With this growing awareness, there is a greater potential for remanufacturing, where the leaser is looking to get the best return on their investment by extending the life of a product. Technical and process development, such as increased automation in remanufacturing helps to reduce the costs of the final product, improving competitiveness with newly manufactured products. However, there is still a lack of skills and awareness of remanufacturing, especially amongst SMEs. This suggests a need to introduce these practices in the training of designers and engineers so that they can bring expertise to the workplace and normalise the practice of remanufacturing.
Future work
As part of the programme of developing its long-term sustainability of the project, work continues on the dissemination of the project findings and learning materials, at both academic conferences and practitioner events, for example Coventry’s Green Business Network.
Further Details
Further details of the project may be found on the RemanPath project website or by contacting Professor Sally Dibb or Dr Helen Roby.